Construction Talk – Top 5 Warehouse Building Issues
If you’re planning to construct a warehouse, here are five things to consider.
Warehouse construction involves some very specific considerations. Here are five issues you’ll need to confront if you’re contemplating this type of project:
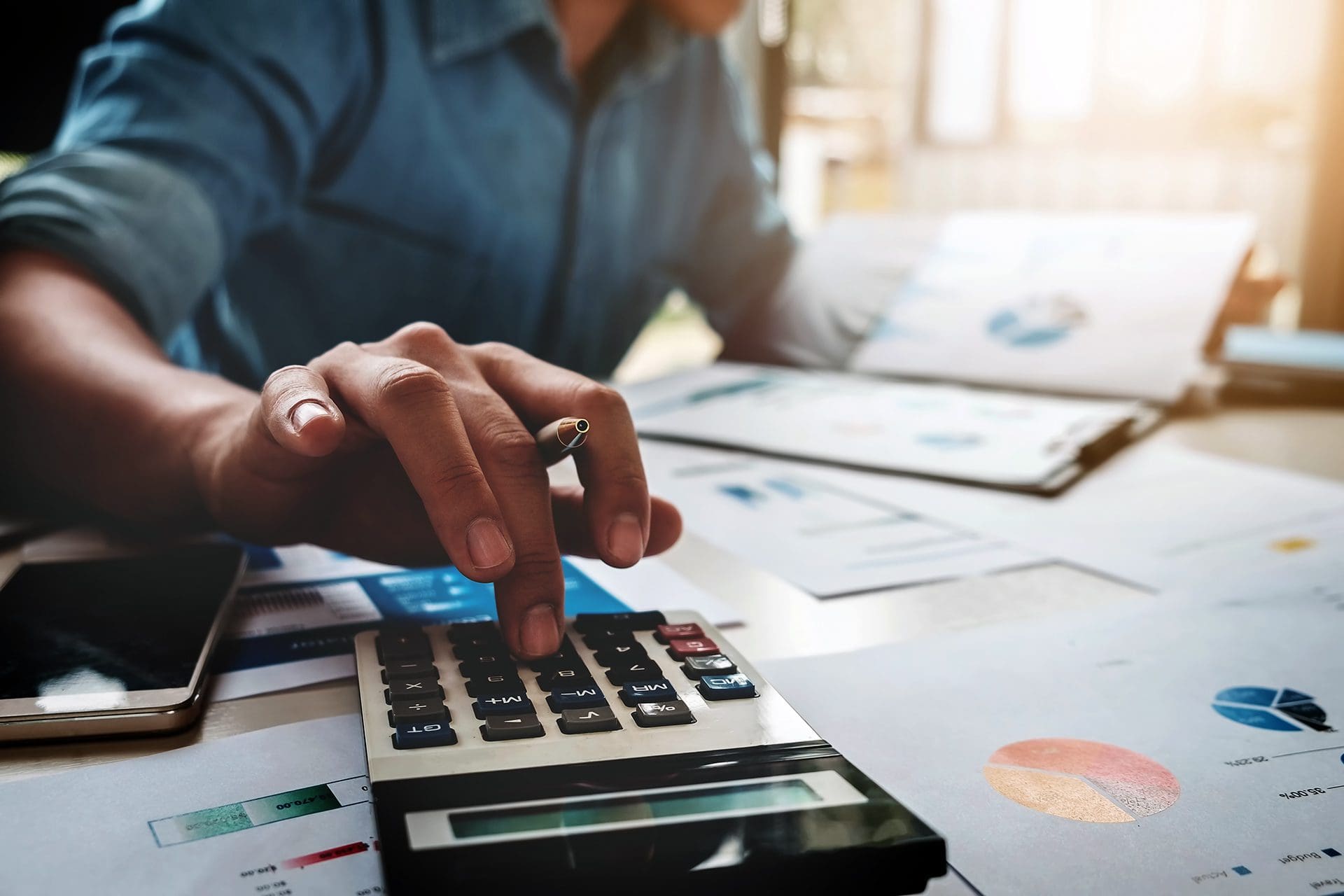
1. Warehouse Construction Costs
Whether you’re building to occupy or to lease, you’ll want to know the real costs of building and maintaining your warehouse—including the long-term costs that may not be obvious.
Labor and materials costs can vary dramatically depending on where you build. And there will likely be local, county, state and federal taxes and fees to consider. Environmental regulations and other restrictions could add significantly to your expenses. Insurance costs will vary too, depending on local risk factors such as fire, flooding, earthquakes and hurricanes. On the flipside, some locales offer tax incentives to encourage you to build. To get a complete picture, you’ll want to inquire with state, county and local regulatory agencies, franchise tax boards, county assessors, and insurance representatives.
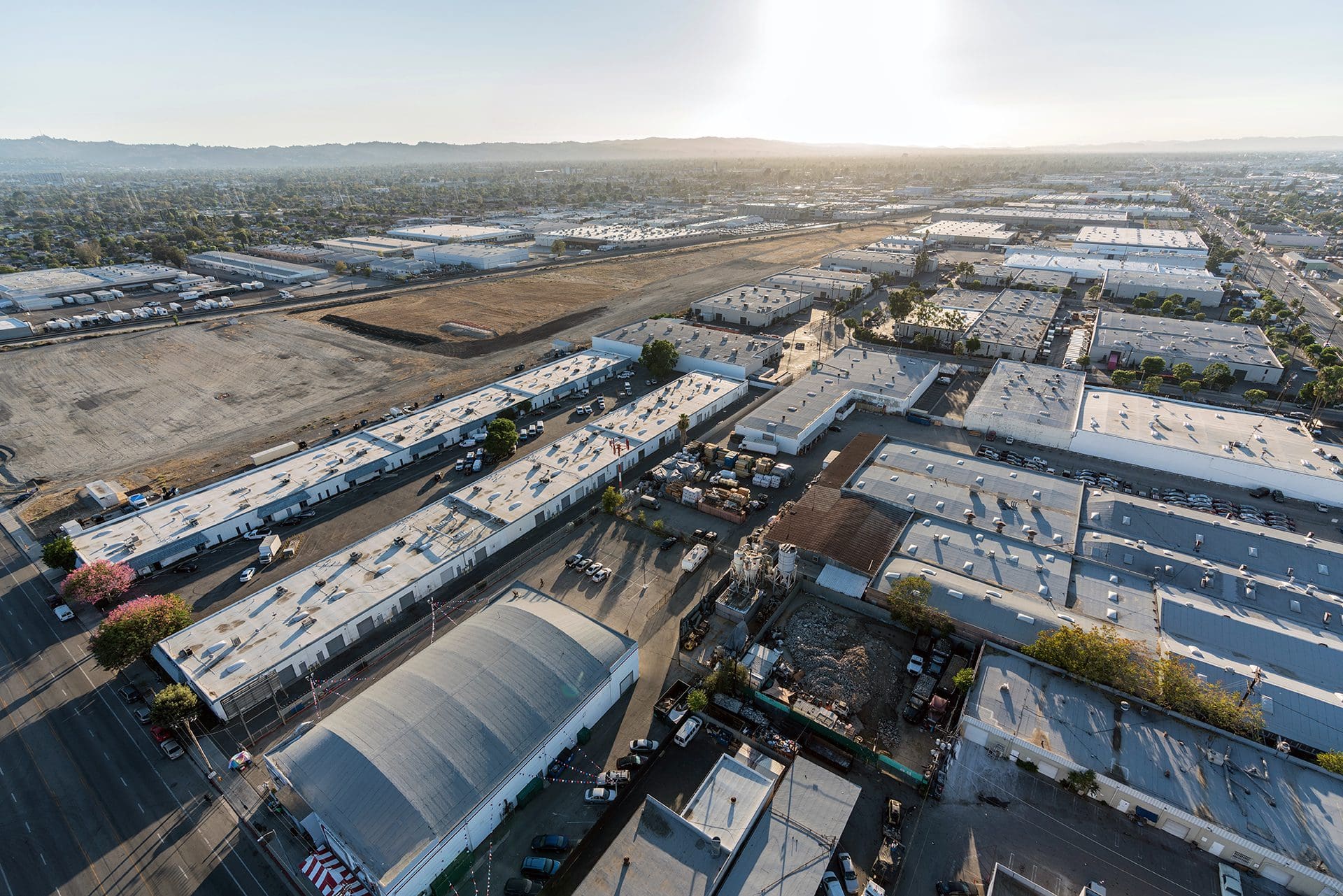
2. Warehouse Location
It makes sense to locate a warehouse where other warehouses are. These areas are usually already zoned for the purpose and typically feature competitive land prices. But for your purposes, other factors may be even more important. A primary consideration should be the structure’s proximity to the entities you will deal with, such as:
Customers
If you’re operating a business, your customers are priority number one. Make it easy for them to do business with you. They expect and deserve fast, convenient access to your products and services. You’ll want to consider their needs in choosing your location. If your customers are scattered across the country (or the world) multiple strategically located warehouses may be the solution.
Suppliers
Proximity is also important for the companies that supply your business. Having them reasonably close reduces delivery time and expenses. It also reduces the risk of supply chain disruptions. If your suppliers are in the Asian-Pacific (APAC) region, having a warehouse on the West Coast of America could be the best option. If they’re in Mexico, locating close to the border might make sense.
Transportation
How will your goods and supplies be transported? By ship? Rail? Truck? Parcel service? Or (likely) some combination of these? It’s a good idea to game out the actual process of transportation from original source to end user—for your products as well as supplies. Then select a location that accommodates all phases conveniently. That may mean being close to a port, a trucking corridor, a rail terminal, or—best of all—an intermodal transit hub, where goods can be transferred easily from one mode to another.
Workforce
If you’re planning to operate the warehouse, you’ll need to recruit people to work in it. And they’ll need to live somewhere within commuting distance. You’ll want to Investigate the demographics of the area you’re considering—including population density, average income, housing prices, unemployment rate, etc. Remote areas may offer cheaper land prices. But locating in the middle of nowhere could pose a problem when it comes time to hire staff. You may need to pay more to locate near a population center.

3. Warehouse Construction Permits
This can be the most aggravating part of any construction project. Local building departments typically have very extensive and specific requirements that may seem arbitrary—and can take months to comply with. Permit fees are often based on the valuation of the project, so that must factor into your cost estimates. If you’re building in an unincorporated area, you will still have state and county requirements to satisfy. The best option in most cases is to work with a contractor that’s familiar with the bureaucratic landscape, with a proven track record of success. They can handle the red tape while you concentrate on the big picture.

4. Accelerated Timelines
Sometimes a project owner or the contractor needs to speed up the construction schedule for one reason or another. The occupant may need the facility sooner than expected; weather may force a schedule adjustment; labor or supply issues may require a change. Whatever the reason, accelerated timelines can add to construction costs through overtime pay and legal expenses.
5. Warehouse Design/Layout
How your warehouse is laid out will determine its effectiveness and efficiency. It makes sense to take some extra time planning this part of the project. Fortunately, there are apps available to help you do that. SmartDraw and AutoCad offer software specifically for warehouse layout and design—so you don’t have to start from scratch.
Most people think of warehouses as storage space. But experts suggest that storage should only comprise 22 to 27 percent of your floorspace. The rest will be needed for reception, packing, picking, loading, unloading, equipment storage, office space and other work areas.
While floorspace may be limited, vertical space can provide the additional storage room you need. Don’t be reluctant to build upward—and use every cubic foot. Aisles should be wide enough to accommodate forklifts, pallet jacks, or any other equipment you may need to use. That usually means at least 12 to 13 feet.
And when you’ve devised your best layout plan—give it a test run.
These are some basic considerations that pertain to most warehouse construction projects. But it’s wise to work with a construction firm that already knows the ins and outs.
As with all things in life, there is no substitute for experience.
The Fleming Construction Group are Warehouse Construction Experts!
Check Out Our Featured Projects Page to View Our Portfolio
